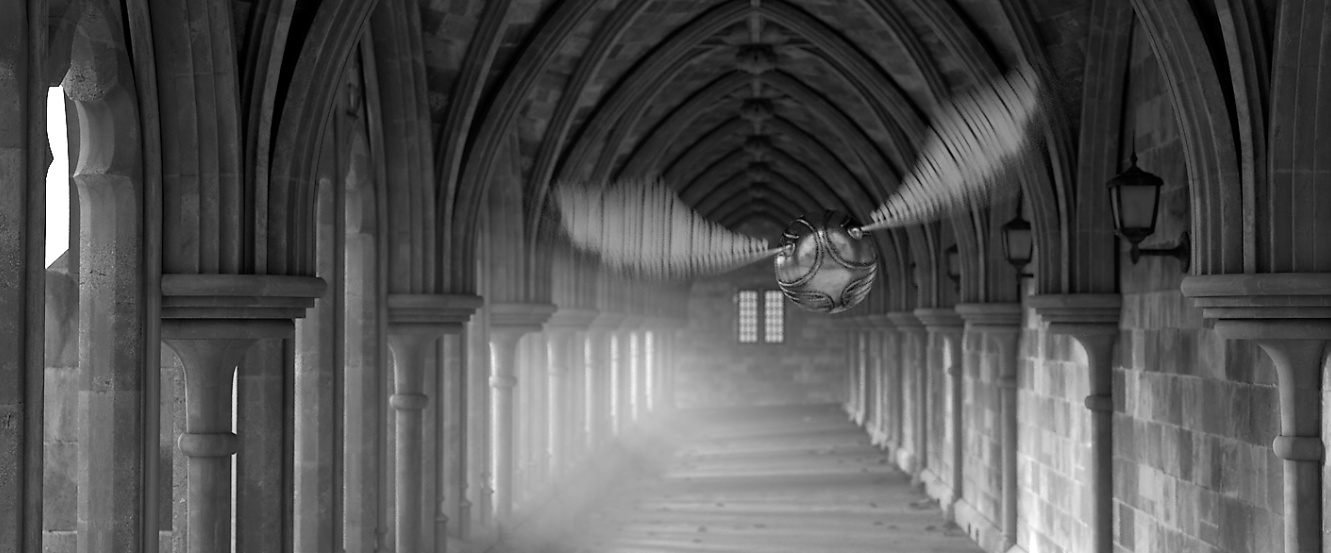
Cerbera
Community Staff-
Posts
17,811 -
Joined
-
Days Won
698
Content Type
Profiles
Blogs
Forums
Gallery
Pipeline Tools
3D Wiki
Plugin List
Store
Downloads
Videos
Everything posted by Cerbera
-
I think that is for monetization reasons. Chris / RL used to have 2 YT channels, one for the live stuff, and another one that used to be used to archive past streams just before the new one went live. But recently that has been limited to only older series, new feature / version presentations and the odd specialised tutorial. I think the complete archive of episodes is probably only available to his patreons. Not sure that is 100% correct, but that does seem to be the way it works now. CBR
-
Oh THAT's where they're hiding that these days ! CBR
-
Oh I see what you mean. Hmmm. not sure about the 'right' way to do that, but you can stop the anim at the frame you want and do a current state to object on the hair, which will get you a hair-renderable spline of the current state, but then of course you have lost the parametricity and subsequent dynamics without linking it to a new Hair object, which I am not currently sure how to do, but seem to recall it is a doable thing ! CBR
-
You should be able to simply turn hair dynamics off in the object settings, so your question mentioning disabling dynamics has confused me somewhat. Additionally, you can use any of the hair styling tools, which has much the same effect and auto-disables dynamics. CBR
-
Carry the Aim constraint target over to an instance or clone?
Cerbera replied to EAlexander's topic in Cinema 4D
I would put additional aim constraint tags on the instances, which should override the one on the original provided they appear below it in the OM. OR if that didn't work I would hide the original off-camera somewhere, and remove the aim constraint from it but not its instances. For nested hierarchies like this it might mean making instances of the things inside the main null rather than the parent null itself. CBR -
I don't disagree with a lot of that ! 🙂 Perhaps it is my daily use of it that negates that stage. I must admit to having other preferred ways of creating arcs and arches too ! The thing I most still dislike about it is the amount of times I have to drop it to use another tool that does what I need properly ! Primarily this is acting on more than 1 edge at a time, and because it can't do continuous line cuts. It does also infuriate me sometimes with its reluctance to ctrl-grab edges in favour of creating a new point which I then have to escape from, or undo to remove. So yes, I certainly concur it is some way off perfect ! But it does have redeeming qualities I enjoy / utilise (quad strip mode / reproject function, helpful tweak modes etc) so I tend to overlook or just not use the functions it has that frustrate me. CBR
-
That surprises me to hear. For me it's really not that bad - I use it every day for the retopo's and it does a mostly solid job of that, with only a few little remaining eccentricities and behaviours that wind me up occasionally.
-
You have to understand that poly pen is a composite tool and because it is trying to do so many things at once and has so many different modes of working, the modifier keys are all taken up offering additional tool functions rather than constraining things straight. For example, the Line Cut dedicated tool DOES have shift-to-constrain-straight functionality because the modifier keys aren't needed for other things and the tool has just one main function. With all the snapping options we have, plane and polygon primitives that arrive straight out-of-the-box, and, as Hrvoje mentioned, helpers like dynamic guides I don't often find myself wishing PolyPen would do straight lines itself. CBR
-
Yeah, PV = Picture Viewer. You shouldn't actually even NEED an RS tag on the particle group - they should appear in render right out of the box (preusming they have appeared in the scene, lols). Tag only needed if you want additional options there, without it, it defaults to mode 'optimised spheres' I am told... CBR
-
You gotta cache those puppies to get them out to PV full render... Do this in the Particle Group Cache tab. Or here's Chris, showing the other methods. CBR
-
Courtesy of Silverwing VFX, I think this might help with Octane / mograph colours... CBR
-
You can hold ALT as you drag the sliders to radically slow them down ? CBR
-
I hope you are not inferring what was not implied ! I cough only in reference to the surprising obviousness at you not mentioning liquids as being an area still missing ! CBR
-
*cough* liquid sim ?? That's one big area we are still 'missing'... CBR
-
The OM is arguably one of Cinema's greatest strengths, and its userbase are rather attached to it, not to mention, used to it, so I think it makes sense to introduce such a powerful new system via an innately familiar interface, and using its workflows and structures. I like having all the particle stuff there in the OM where I can always see it and (mostly) what it is doing without having extra windows floating about. That's not to say I couldn't also see it working in a nodal context, but I have to say I kinda like it where it is... CBR
-
It's a wonderful release, adding a boatload of functionality to simulation and a solid first step to bringing our particles up to date, and fully integrated with other simulation components - as Chris was at pains to point out the possibilities now are mind-boggling ! I think a lot of people will be very happy with this release, except possibly the guys who make X-Particles; it will be interesting to see where they pivot next. Of course all the attention is rightly focused mainly on the particles, but I was pleased that there have been good updates in other areas, a few of my own suggestions have been added to modelling functionality, and RS got a lot of love and improvements, not least being the toon shader stuff. The new Connectors functionality and workflows are so much easier to work with than the old system, so that is very welcome too. So all in all, I am loving this release... CBR
-
I'm getting weird white strips in my textures (PLEASE HELP)
Cerbera replied to David Cowell1's topic in Cinema 4D
This can also happen when there is no physical thickness on the label. Adding a tiny amount will usually resolve this as well. CBR -
In a lot of ways I agree with @bezo who questions if lofts are the best thing to use for this. TBH it is quite an unconventional use of a loft in the first place ! Ordinarily I would say it's not ideal, but I am aware there may be perfectly valid reasons why you might need it to be splines, or procedural etc etc... But we can still apply polygon rules when using splines, and if we want certain areas curved and others very sharp, then we just need to make our splines do the right thing, which in your case would be this... So straight bits get no intermediate points, curves get evenly distributed ones, and sharp corners get control points either side of the corner. But of course that is quite difficult (and perhaps impossible without recourse to nodal spline creation) to get procedurally. Which is a shame, because under an Extrude I'm fairly sure a manual spline like, with default interpolation that is giving you exactly the shape you need, and if you don't need to care about cap topology because it's flat, then that alone might be enough ? CBR
-
It's not my area of specialisation, but I watch developments with interest. I think most people still consider Maya the ultimate for rigging, but I don't think Cinema is doing too badly in that department either. We recently improved quite a lot about weights and symmetry workflows, and before that Character Object and C-Motion were good leaps forward in setting up these things quite quickly without a great deal of in-depth knowledge... I found Noseman's recent 4 hour rigging series on the Maxon training team's YT channel particularly helpful in understanding all the rigging basics and possibilities open to us, so maybe it would help you catch up too... Or for even more detail, and a better focus on character rather than than machine riggings, there was this excellent (and exhaustively thorough) series that preceded it. CBR
-
For me, reversing the point order on just the segments where it is wrong works every time... Here's an inexplicably screwed one... Yet if I reverse the point order in the lower segment then voila... I can't tell you why it happens tho - that remains utterly baffling ! In the first example above we can see the spline direction is the same for both segments, so why the cloner does that with it remains a mystery to me. For me, instancing that fixed spline preserves the correction (instanced version on right there), so you would need to upload a scene file which will show us what might be different in your setup vs mine... CBR
-
Not that I am aware of - I guess that sort of functionality has been made somewhat less needed because of the Placement / Dynamic Placement tools, which although not letting you draw stuff directly on objects, does at least allow you to put them there after creation. Edit: Oh yeah - scatter ! CBR
-
I thought HUD is part of layout isn't it ? So if you save yours as one of those it can be loaded at any time into any file, right ? CBR
-
No no, in fact I'd say FBX was superior to OBJ in every way, except possibly wider compatibility with really old software !
-
I think the more apposite question might be 'Why is OBJ so much more inefficient than every other format?' !! It's true OBJ files can be huge. I don't know specifically why this is, but feel sure it must have something to do with 'legacy', given that OBJ is a very old and 'first gen' format that should have been retired a while back, but (presumably) for backwards compatibility and 'library' reasons, hasn't been. CBR